What is Porosity in Welding: Secret Variables and Their Impact on Weld High Quality
What is Porosity in Welding: Secret Variables and Their Impact on Weld High Quality
Blog Article
Porosity in Welding: Identifying Common Issues and Implementing Ideal Practices for Prevention
Porosity in welding is a prevalent concern that usually goes undetected till it triggers considerable problems with the honesty of welds. This common issue can compromise the stamina and longevity of bonded frameworks, posing safety dangers and bring about costly rework. By comprehending the origin causes of porosity and carrying out reliable prevention techniques, welders can dramatically improve the high quality and dependability of their welds. In this conversation, we will certainly explore the essential aspects adding to porosity development, analyze its detrimental effects on weld performance, and go over the ideal techniques that can be adopted to reduce porosity incident in welding processes.
Typical Root Causes Of Porosity
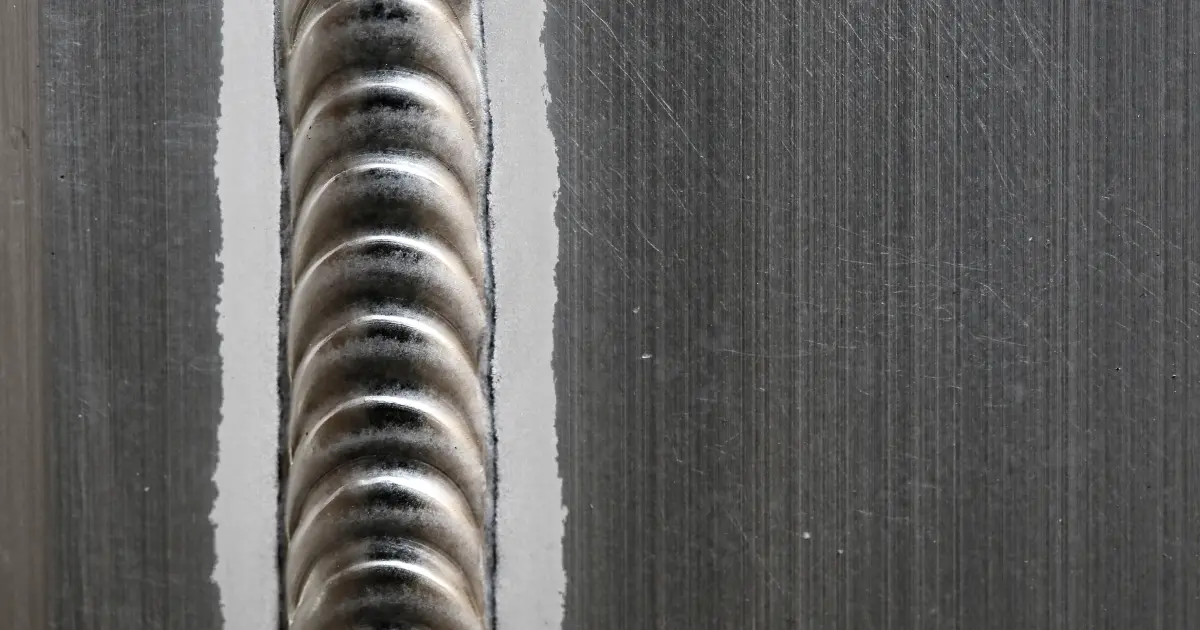
Making use of unclean or damp filler products can present contaminations right into the weld, adding to porosity problems. To alleviate these typical causes of porosity, extensive cleaning of base metals, proper shielding gas selection, and adherence to optimum welding criteria are crucial techniques in attaining high-grade, porosity-free welds.
Influence of Porosity on Weld High Quality

The existence of porosity in welding can significantly endanger the structural stability and mechanical residential or commercial properties of bonded joints. Porosity creates gaps within the weld metal, deteriorating its overall stamina and load-bearing ability.
One of the key repercussions of porosity is a decline in the weld's ductility and strength. Welds with high porosity degrees tend to display reduced impact toughness and reduced capability to deform plastically prior to fracturing. This can be particularly concerning in applications where the bonded parts go through vibrant or cyclic loading problems. Porosity can restrain the weld's ability to efficiently send pressures, leading to premature weld failure and prospective safety and security hazards in vital frameworks. What is Porosity.
Best Practices for Porosity Prevention
To boost the structural stability and top quality of welded joints, what certain actions can be executed to lessen the event you can find out more of porosity during the welding process? Utilizing the proper welding technique for the certain product being bonded, such as adjusting the welding angle and gun setting, can additionally prevent porosity. Regular assessment of welds and prompt removal of any issues determined during the welding procedure are essential practices to stop porosity and generate high-quality welds.
Value of Appropriate Welding Strategies
Implementing proper welding techniques is critical in making sure the architectural stability and high quality of bonded joints, developing upon the foundation of efficient porosity prevention steps. Welding techniques directly impact the overall strength and durability of the welded structure. One key facet of correct welding methods is preserving the appropriate heat input. Too much warmth can cause boosted porosity because of the entrapment of gases in the weld pool. Alternatively, inadequate warm may result in insufficient blend, producing potential powerlessness in the joint. In addition, utilizing the suitable welding parameters, such as voltage, existing, and travel speed, is critical for accomplishing sound welds with very little porosity.
Moreover, the click this site selection of welding process, whether it be MIG, TIG, or stick welding, must straighten with the particular needs of the project to make sure optimum results. Correct cleaning and prep work of the base steel, in addition to picking the right filler product, are additionally vital components of pop over to these guys skilled welding strategies. By adhering to these finest techniques, welders can reduce the danger of porosity formation and produce top notch, structurally audio welds.
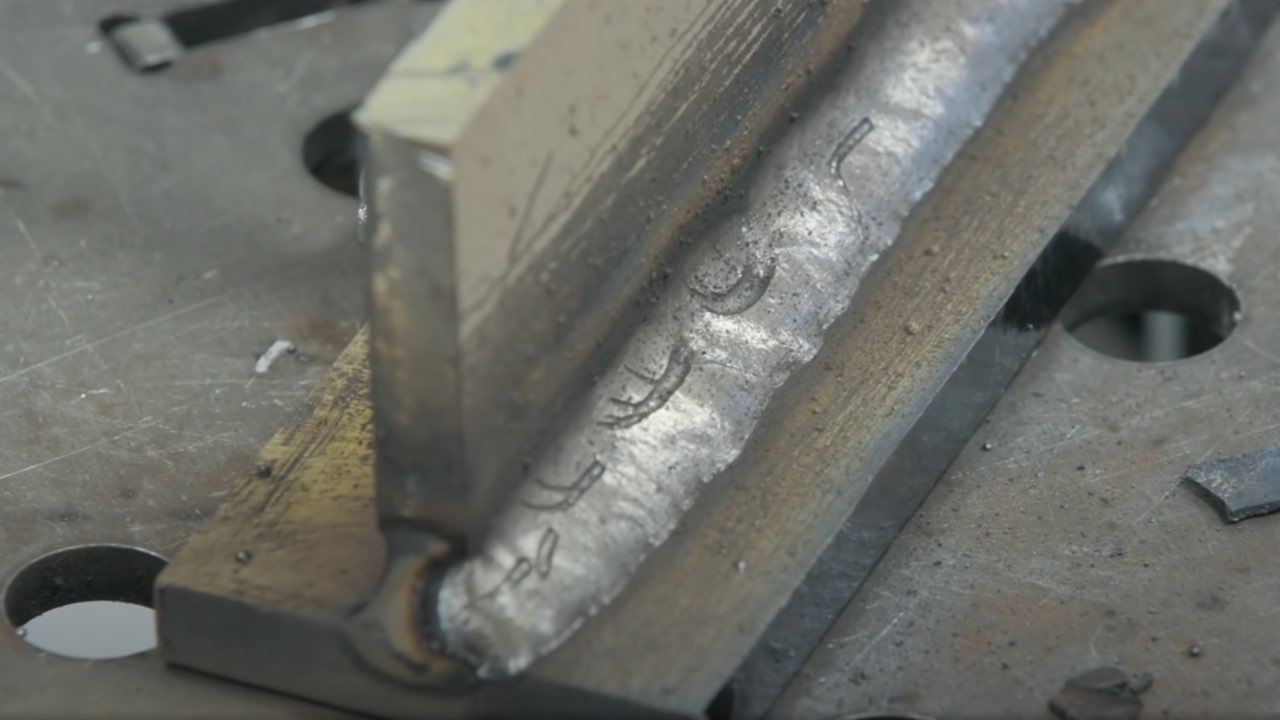
Checking and Top Quality Control Actions
Quality control measures play a critical role in validating the honesty and integrity of welded joints. Testing procedures are necessary to discover and stop porosity in welding, making sure the stamina and sturdiness of the end product. Non-destructive screening techniques such as ultrasonic testing, radiographic testing, and aesthetic assessment are frequently utilized to identify possible flaws like porosity. These methods permit the analysis of weld top quality without jeopardizing the integrity of the joint. What is Porosity.
Post-weld examinations, on the other hand, evaluate the final weld for any type of issues, including porosity, and confirm that it satisfies defined criteria. Applying a comprehensive quality control plan that includes extensive screening treatments and examinations is extremely important to lowering porosity concerns and making certain the total high quality of welded joints.
Verdict
In verdict, porosity in welding can be an usual concern that influences the top quality of welds. By determining the typical sources of porosity and executing best techniques for avoidance, such as appropriate welding methods and testing measures, welders can ensure premium quality and reliable welds. It is essential to focus on prevention approaches to decrease the incident of porosity and maintain the honesty of welded structures.
Report this page